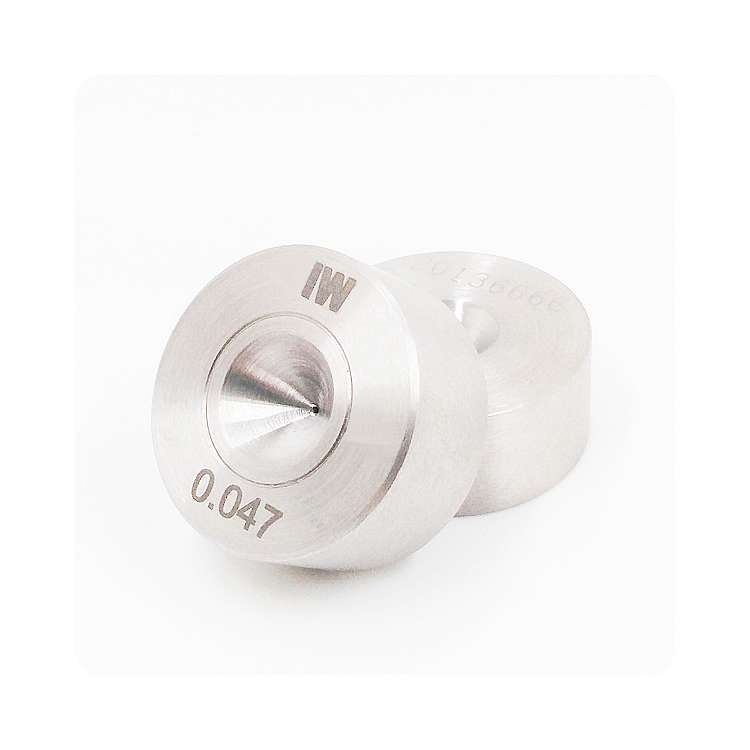 |
Types and uses of wire drawing molds |
1. Definition of wire drawing die
Usually refers to various molds for drawing metal wires, as well as drawing dies for drawing optical fibers.
In the center of all drawing dies, there is a hole of a certain shape, such as a circle, a square, an octagon or other special shapes. When the metal is pulled through the die hole, the size becomes smaller and even the shape changes.
2. Types of wire drawing dies
(1)Steel mold
When drawing soft metals (such as gold and silver), a steel mold is sufficient, and the steel mold can have multiple holes with different apertures.
(2)Carbide mold
The drawn steel wire (steel wire) generally uses a cemented carbide mold. The typical structure of this mold is: a cylindrical (or slightly tapered) cemented carbide core is closely embedded in a circular steel case In the inner hole of the mold core, there are a bell radius, an entrance angel, an approach angle, a bearing and a back relief.
(3)Wire mold
For drawing non-ferrous metal wires, such as copper and aluminum, wire drawing dies similar to wire dies are also used, and the shape of the inner hole is slightly different.
(4)Polycrystalline mold
The fine wire can be used in polycrystalline molds (man-made diamonds), as well as drawing dies in natural diamonds.
3. Uses of wire drawing dies
Wire drawing dies are widely used, such as high-precision wire materials used in electronic devices, radar, television, instrumentation and aerospace, as well as commonly used tungsten wires, molybdenum wires, stainless steel wires, wire and cable wires and various alloy wires. The drawing die is drawn out. Diamond wire drawing die, because of using natural diamond as raw material, has strong abrasion resistance and extremely long service life.
4. Material of wire drawing die
After decades of development, many new drawing die materials have appeared.
According to the type of material, the wire drawing die can be divided into: alloy steel die, hard alloy die, natural diamond die, polycrystalline diamond die, CVD diamond die and ceramic die.
In recent years, the development of new materials has greatly enriched the application range of wire drawing dies and increased the service life of wire drawing dies.
(1) Alloy steel
Alloy steel molds were early materials for wire drawing dies. The materials used to make alloy steel molds are mainly carbon tool steel and alloy tool steel. However, due to the poor hardness and abrasion resistance of alloy steel molds and the short life, they cannot meet the needs of modern production. Therefore, alloy steel molds were quickly eliminated. In the current production and processing, alloy steel molds are almost invisible.
(2) Hard alloy
The cemented carbide mold is made of cemented carbide. Cemented carbide is a tungsten-cobalt-based alloy whose main components are tungsten carbide and cobalt.
Tungsten carbide is the "skeleton" of the alloy, which mainly plays a hard and wear-resistant role; cobalt is the bonding metal and the source of alloy toughness. Therefore, compared with alloy steel molds, cemented carbide molds have the following characteristics: high wear resistance, good polishing, small adhesion, low friction coefficient, low energy consumption, high corrosion resistance, these characteristics make cemented carbide The wire drawing die has a wide range of processing adaptability and has become the most commonly used wire drawing die.
(3) Natural diamond
Natural diamond is an allotrope of carbon, and the mold made with it has the characteristics of high hardness and good wear resistance. However, natural diamond is relatively brittle and difficult to process. It is generally used to make wire drawing dies with a diameter of 1.2 mm or less. In addition, natural diamond is expensive and scarce in supply. Therefore, natural diamond molds are not the economical and practical drawing tools that people eventually seek.
(4) Polycrystalline diamond
Polycrystalline diamond is made by carefully selecting high-quality artificial diamond single crystals with a small amount of binders such as silicon and titanium, and polymerizing under high temperature and pressure conditions.
Polycrystalline diamond has high hardness and good abrasion resistance. Compared with other materials, it has its own unique advantages: due to the anisotropy of natural diamond, during the drawing process, when the entire hole is surrounded by holes Under working conditions, natural diamond will wear preferentially at a certain position of the hole; while polycrystalline diamond is polycrystalline and has isotropic characteristics, thereby avoiding uneven wear of the mold holes and out-of-round mold holes.
Compared with cemented carbide, the tensile strength of polycrystalline diamond is only 70% of common cemented carbide, but 250% harder than cemented carbide. In this way, polycrystalline diamond molds have more advantages than cemented carbide molds. . The wire drawing die made of polycrystalline diamond has good wear resistance, uniform inner hole wear, strong impact resistance, high wire drawing efficiency, and the price is much cheaper than natural diamond. Therefore, polycrystalline diamond dies are currently widely used in the wire drawing industry.
(5) CVD (chemical vapor deposition) coating
CVD (Chemical Vapor Deposition) coating wire drawing die is a newly developed new technology. The main method is to coat diamond film on the carbide drawing die.
Diamond film is a pure diamond polycrystal. It has the advantages of single crystal diamond's smoothness and temperature resistance, as well as the abrasion resistance and low price of polycrystalline diamond. Effect, its widespread use will bring new vitality to the wire drawing industry.
(6) High-performance ceramic materials
High-performance ceramic materials have the characteristics of high hardness, good abrasion resistance, strong chemical stability, high-temperature mechanical properties, and difficulty in bonding with metals. They can be widely used in the processing of difficult-to-machine materials. |
|
|