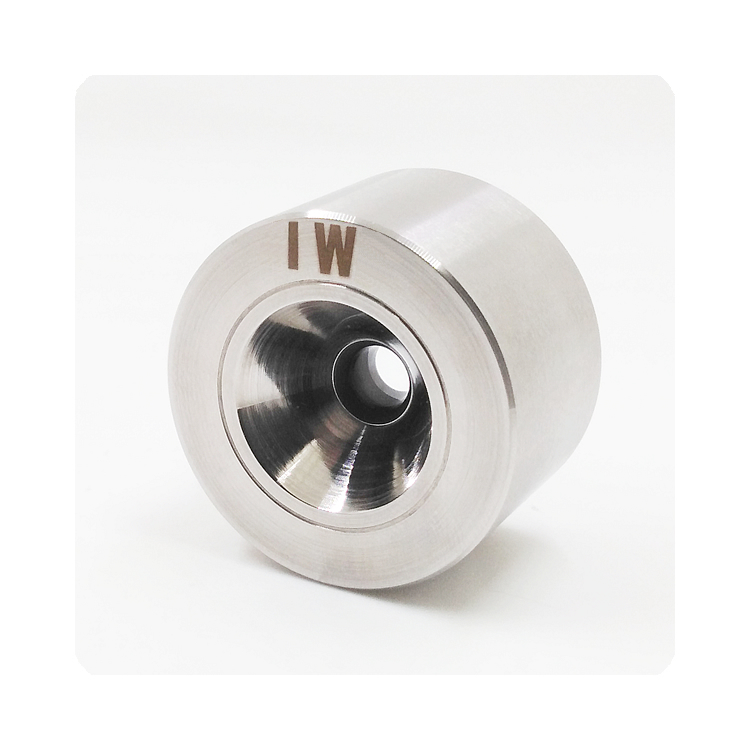 |
Processing method of polycrystalline diamond drawing die |
Laser machining and electrochemical machining of polycrystalline diamond drawing die
1. Laser processing
Laser processing is to use the energy of light through the lens to focus on the focus of high energy density, relying on the photothermal effect to process various materials.
Laser and laser processing system and other basic equipment.
In the 1960s, Lichuan ruby laser processing of natural diamond drawing die was the first success in China.
Later, it was applied to the processing of compression area and sizing area of polycrystalline diamond drawing die.
Practice has proved that the performance of ruby laser drilling machine mainly depends on high-quality ruby. The output spot of ruby should be round and the center point should be stable and clear.
The leap in laser processing of wire drawing dies is due to the advent of Yunzhou ryag material (yttrium aluminum garnet) and continuous laser with microcomputer processor.
By inputting the pre programmed die hole program into the computer, the rough machining of the whole die hole can be completed automatically. The die making process is greatly simplified and the standard shape of the die hole is ensured.
The range of laser piercing is q0.01-0.1mm, the ratio of hole depth to aperture can reach 50-100, and the piercing efficiency is high. It is suitable for rough machining of small hole drawing die within 1 mm.
2. Electrochemical machining
Electrochemical machining (ECM) is formed by dissolving the electrochemical cathode of Lichuan metal in the electrolyte and adding t to the upper part.
Because polycrystalline diamond is composed of many kinds of metals and diamonds, the reaction between electrodes in electrochemical machining is very complex, so this method is not suitable for the processing of polycrystalline diamond drawing die. |
|
|